2024.10.22
日本初の水中ポンプ専業メーカー、櫻川ポンプ製作所【2】生産本部は日々改善がモットー 進化し続けるモノづくりの現場。株式会社櫻川ポンプ製作所は、生産工程において常に改善に取り組み、効率化の向上を図ることで、より良い製品を生み出している。現場の改善は、働きやすさにもつながる重要課題だ。
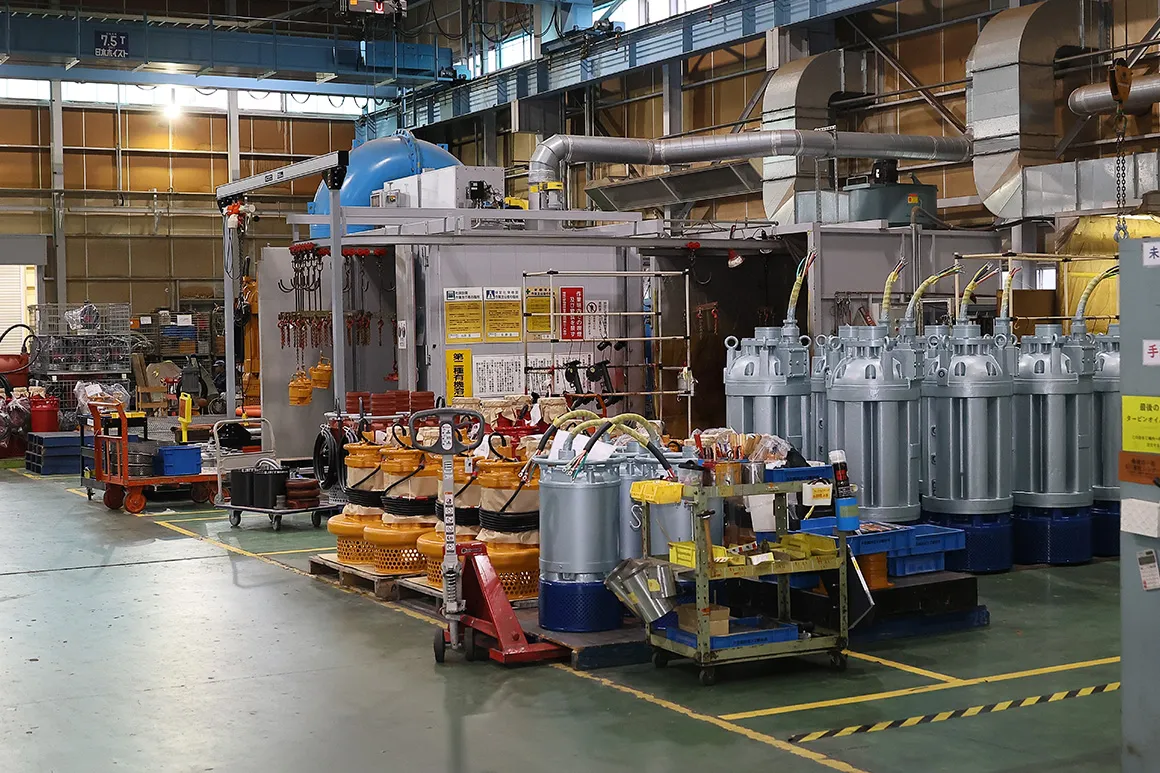
高品質でありながら低コストを目指す
櫻川ポンプ製作所の福井工場は組織上、生産本部、技術開発部、ブラッシュピット事業部、福井営業所に分けられる。生産本部には製造課、品質保証課、生産管理課、メンテナンス課があり、それらを統括しているのが岩田友典取締役上席執行役員 生産本部 本部長だ。まずは生産方式や生産目標を聞いた。
岩田「弊社の水中ポンプは多品種少量生産なので、1人の作業者で製品を完成させる1人屋台生産方式を採用しています。工場は週休2日制で、月の生産目標台数は700台です。技術は新しい製品を生み出し、営業は売り込むのが仕事ですが、工場は品質の高い商品を、コストを抑えながら生産するのが使命です。生産本部は利益の根源を生み出す部門です。生産工程、調達においていかにコストを抑えるかを常に考えています。あとはサプライチェーンの維持ですね」
岩田友典取締役上席執行役員 生産本部 本部長
水中ポンプは、およそ何点の部品で構成されているのだろうか?
岩田「どこまで細かく分けるかにもよりますが、大きく分けるなら、モータ、ローターシャフト、ベアリング、メカニカルシール、ケーシング、インペラ(羽根)など、10点くらいの部品でできています。差別化が難しい業界ですが、弊社の製品は『丈夫で長持ち』を最大の特徴としています。主力はオートポンプです。あとは大手のメーカーさんがやりたがらない、ワンオフ(オーダーメイド)やカスタマイズにもフレキシブルに対応できます」
水中ポンプの構造は、モータが収まる上側と水を吸い込むインペラがある下側に大別される
今、生産本部で取り組んでいる課題としては、内製化を挙げる。
岩田「5.5kWくらいまでのモータを、年内を目途に内製化する計画です。内製化にあたっては社内的な工数が増えますので、人や場所の問題を解決しなければなりません。人は簡単に増やせないため、一部の工程を自動化するなどして生産効率を上げ、対処する予定です」
内製化のメリットは、外部委託に伴うコストの低減、生産効率の向上だけではない。
岩田「モータの自社生産が可能になれば、いろいろな実験、検証、基礎研究も行えるため、ナレッジの蓄積が見込めます。これは大きなメリットですね」
働きやすい環境に配慮
製造課の社員一人ひとりが高いポテンシャルを常に発揮できるよう、段取りや仕事量に気を配っているのが齊藤健太郎課長だ。
齊藤「弊社は1人屋台生産方式を採用しています。実際は向き不向きもあるため、難しいですが、誰もが、どんな水中ポンプでも組み立てられるオールマイティーな生産が理想です」
製造課の齊藤健太郎課長
水中ポンプを組み立てる際、どのあたりが特に難しいのだろうか?
齊藤「水の中に沈めて使う機械なので、防水性が重要です。メカニカルシールを用いて水が入らないようにしていますが、組み付けの際にゴミが入ると水漏れの原因になります。そこは細心の注意を払って作業するよう指示しています」
組み付け後は、どのような検査を行っているのだろうか?
齊藤「大型の水中ポンプは全品、小型の水中ポンプは抜き打ちで仕様通りの性能が出ているかチェックしています。水の中に沈めて、実際に負荷をかけて稼働させるわけです。製品によってはテスト後に塗装を行います。濡れていると塗装ができないため、エアで水滴を飛ばします。この工程を自動化、つまりオートブローを採用することによって省力化を図り、ほかの工程に人員を配置できるよう、現在、鋭意取り組んでいる最中です」
生産現場はクリエイティブ
生産現場で陣頭指揮を執っているのが、製造課の石黒崇嗣主任だ。
石黒「弊社は多品種少量生産という話があったと思いますが、誰もが何も見ずに作業できるわけではありません。以前は一子相伝の技みたいな雰囲気があったり、知識量でマウントを取るベテランがいたりしましたが、 私が主任になってからそんな空気を変えるため、バーコードを読むと手順書が出てくる仕組みをつくりました」
実際に作業員がその手順書を見て組み立てて、何か不備があったら随時改定しているという。
石黒「工場は毎日、同じことをやっているんだろう、と思われがちですが、それは間違いです。10秒かかっていた作業が9.5秒でできるようになるだけで全然違います。ちりも積もれば山となります。だから日々、新しいことを考えています。意外とクリエイティブですよ」
製造課の石黒崇嗣主任(左)
石黒主任と話していると、仕事が楽しい、水中ポンプが好き! という雰囲気が伝わってくる。実は、今の立場になるまで随分と回り道をしているのだが、その経験が石黒主任の幅を広げたのかもしれない。
石黒「アイデアが通りやすいのでやりがいがあります。例えば、作業員の負担を軽減する装置を思いついたら、作らせてもらえます。今年で40歳になりますが、いつまでもアイデアマンでありたいと思っています」
重い水中ポンプの組み立てを、体に負担なく行える回転作業台を開発。石黒主任のアイデアだ
改善業務を託された若手社員
生産現場にとって"改善"は永遠のテーマだ。製造課の竹内滉貴さんは2023年4~12月、アクティオの「APS道場」に参加した。APSとはAktio Production Systemの略で、トヨタ生産方式(TPS)をお手本にした生産ラインから無駄を排除するための方式である。
竹内さんはAPSの10期生で、最年少だった。具体的にはどのようなことを学んだのだろうか?
竹内「最初の1カ月は、アクティオの三重いなべテクノパーク統括工場でトヨタ生産方式、改善の仕方、改善の目線、事例といったものを学びました。これは基本的に座学です。次の3カ月は実技です。三重いなべテクノパーク統括工場を3カ月かけて改善しました。私が特に力を入れたのが"表示"です。この部品は何に使うのか、誰が見ても分かるようにしました。また、作業場のレイアウトも最適化しました。移動距離、動線を変え、通路も確保しました。これも効果が出ましたね」
座学だけでなく、実際に改善に取り組み、APSを体感することが、本プログラムの特長だ。
竹内「後半の3カ月半は、千葉県にあるアクティオの野田工場で生産管理板を作成しました。日々の進捗、目標、達成を見える化することで、管理しやすくなるだけではなく、作業者のモチベーション向上につながることも分かりました。最後の1カ月半は、アクティオの本社でまとめ作業を行いました。また11期生に向けたテキストの修正にも取り組みました」
製造課の竹内滉貴さん
かなり濃密なプログラムだが、APS道場は参加して終わりではない。自分の現場に戻り、学んだことをいかに実践するかが最大のポイントだ。
竹内「実は製造課の齊藤課長から、課題をいただいています。ポンプの仕上げ工程、具体的には試験・塗装・仕上げの3工程で滞留が発生しがちなので、そこの改善に取り組んでいます。日々、作業員と話し合い、現状把握、問題点の洗い出しを行っています。すると、特に塗装がネックであることが分かってきました。そこの作業に波があり、たまりやすいんですね。今は作業内容を分割して、作業員を増やすことでの解決を目指しています」
塗装工程の人員を増やしたいが、マンパワーには限りがある。そんな課題を解決するひとつの方法が自動化だ。写真は本格導入に向けて試験運転中のオートブロー
「工場には金が落ちている」という言葉がある。徹底した無駄の排除、ひいては生産性の向上が利益を生み、それはやがて顧客へと還元される。
さて、最終回となる次回は、新たな製品を生み出す技術開発部にスポットを当てたい。
※記事の情報は2024年10月22日時点のものです。
【3】へ続く
〈ご参考までに...〉
● 水中ポンプ・水処理機械(アクティオ公式サイト)